Crafting Your Own Metal Embossing Stamp
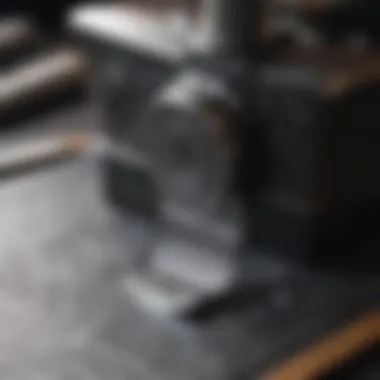
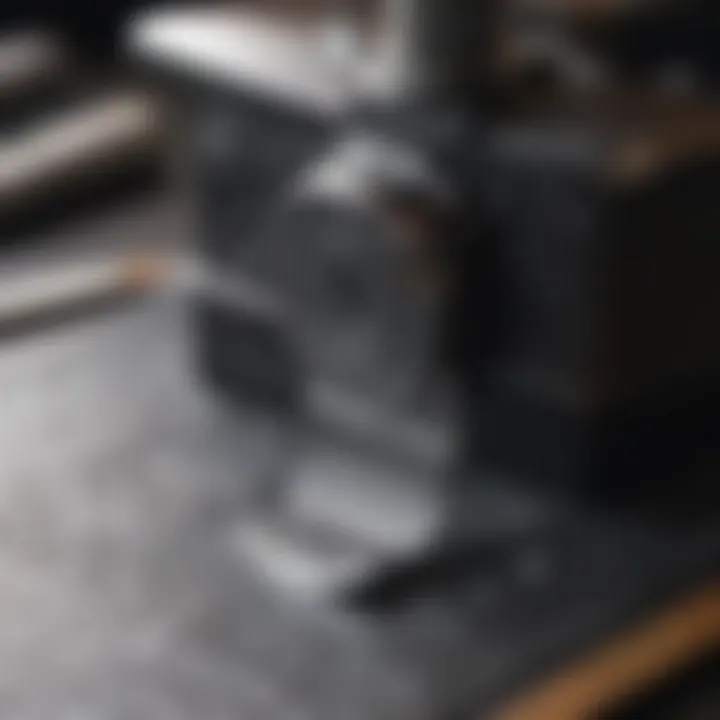
Intro
In the world of craftsmanship and artistry, creating a metal embossing stamp is akin to laying the cornerstone of a creative endeavor. This guide is your compass as you navigate the intricate landscape of metalwork, designed to enlighten both fledgling artisans and seasoned pros alike. Have you ever pondered how artisans etch their unique designs onto leather, paper or fabric? The answer often lies within the tool of their trade: the metal embossing stamp. With the right tools and techniques, this process can transform simple ideas into a tactile reality, giving life to your artistic visions.
Understanding metal embossing is not just about the mechanics; itโs also about the artistry involved in design creation. In this guide, you will come to appreciate the depth of connections that the practice fosters within the design community.
Through this exploration, we will peel back the layers of crafting an embossing stamp, providing insights and practical tips to help you rise from a novice to a seasoned creator. Whether your aim is to create personal projects, approval designs, or even delve into the business aspect of metal embossing, this guide will serve as a valuable resource in honing your skills. Letโs dive into the essentials, laying the foundation for craftsmanship that stands the test of time.
Foreword to Metal Embossing
Metal embossing is an age-old craft that allows artisans to create unique designs and patterns on various metal surfaces. It's a skill that not only involves artistry but also encompasses technical know-how and the use of precise tools. This section aims to set the stage for understanding the nuances of creating metal embossing stamps, laying the groundwork for the more intricate discussions that follow. The importance of this art form cannot be overstated, as it finds applications in myriad fields, from fashion and jewelry making to packaging and branding.
The beauty of metal embossing lies in its transformative power. With just a few tools and a dash of creativity, a plain piece of metal can become an exquisite item, holding personal meaning or commercial value. Itโs a method of imprinting identity, literally and figuratively, onto a material that has adorned both functional and decorative objects for centuries. Through embossing, one can personalize gifts, create one-of-a-kind pieces for retail, or add branding elements that stand out in a crowded market.
Understanding Embossing Techniques
Embossing techniques vary widely, with each method offering its own set of benefits and challenges. Generally, these techniques can be categorized into a few main types:
- Direct Stamping: This is a traditional technique where a metal die is pressed directly into the surface of the material. Itโs relatively straightforward and allows for intricate designs, but it requires significant skill to ensure that the depth and clarity of the impression are consistent.
- Heat Stamping: Another popular method involves applying heat alongside pressure to create the design. This technique can help in softening the metal, allowing for more detailed impressions, though it demands careful temperature regulation to avoid damaging the material.
Each technique comes with its own rhythm and flow, akin to a dance where precision and timing dictate the outcome. Whether one chooses direct or heat stamping often depends on the design complexity, the type of metal, and the desired finish.
Historical Context of Metal Stamping
Metal stamping has a rich history that dates back to ancient civilizations. The earliest forms of metalwork can be traced to cultures like the Egyptians, who used rudimentary tools to create decorative items and utilitarian objects. As civilizations evolved, so did the processes.
In the Middle Ages, techniques refined further with advances in metallurgy and design. It was during this period that embossing began to find its way into everyday items, crossing over from the realm of the elite into common households. Objects such as armor, jewelry, and household utensils bore intricate designs that not only served aesthetic purposes but also denoted social status.
Fast forward to the Industrial Revolution, where mass production changed the landscape of metalworking altogether. The introduction of machinery allowed for precision stamping on an unpreceded scale, making embossed items more accessible. Today, both artisanal craftspeople and large-scale manufacturers continue to push the boundaries of metal embossing, blending age-old techniques with modern innovation. This rich tapestry of history provides a much deeper context for the craft today, reminding us that creating a metal embossing stamp is not just a task but a continuation of a centuries-old tradition.
Essential Tools and Materials
When embarking on the journey of crafting a metal embossing stamp, understanding the essential tools and materials is paramount. Without the right equipment and materials, the process can quickly transform from a creative project to an exercise in frustration. A well-equipped workspace not only enhances your efficiency but also amplifies your potential for creating high-quality, intricate designs. Let's deep dive into the types of metals you will encounter, the necessary hand tools required, and how dies and molds will play a crucial role in your stamp making.
Types of Metal Used
Choosing the appropriate metal is the foundation of producing a successful embossing stamp. Each material comes with its unique set of traits that can affect both the shooting end results and the crafting process itself.
Copper
Copper is a favorite among artisans for many reasons. This metal is highly malleable, allowing for ease when creating detailed designs. Its excellent thermal conductivity is another characteristic that makes it widely beneficial. Unlike some metals that can warp under heat, copper generally holds its shape, making it reliable for intricate stamping details.
One unique feature of copper is the attractive patina it develops over time, which can add character to the finished product. However, this can also be a double-edged sword as it might require polishing to maintain that fresh look.
Aluminum
Aluminum isn't far behind in the popularity contest. It's lightweight and offers corrosion resistance, making it a beneficial choice. One can easily achieve intricate designs without the excessive weight and bulk of heavier metals.
A distinct advantage of aluminum is its affordability, enabling newcomers on a tight budget to experiment without a massive upfront investment. However, it's crucial to note that aluminum might not yield the same sharpness or depth in detail compared to copper or brass, so skillful planning is necessary.
Brass
Brass strikes a remarkable balance between strength and aesthetics. It showcases a beautiful, gold-like appearance that adds visual appeal to any application. Its hardness makes it exceptional for stamps that endure repetitive use, promising longevity.
However, some may find that brass can be less forgiving during the initial carving of designs due to its rigidity. Maintaining and polishing brass also requires consistent care to avoid tarnishing, but the effort often pays off with stunning results.
Necessary Hand Tools
Every craft has its arsenal. The hand tools for metal stamping serve not merely as implements but as extensions of the craftsman's ability to mold their vision into tangible form.
Hammers
A quality hammer is fundamental to this craft. It's not only about brute force, but precision matters for clean impressions. A ball-peen hammer is typically most recommended for embossing tasks; it allows for even distribution of force, yielding clean designs.
Moreover, a well-balanced hammer enables intricate work without tiring your hands excessively. The design of hammers helps to disseminate energy efficiently, treating both the tool and the workpiece with respect.
Files
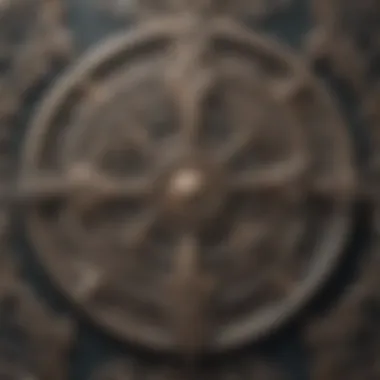
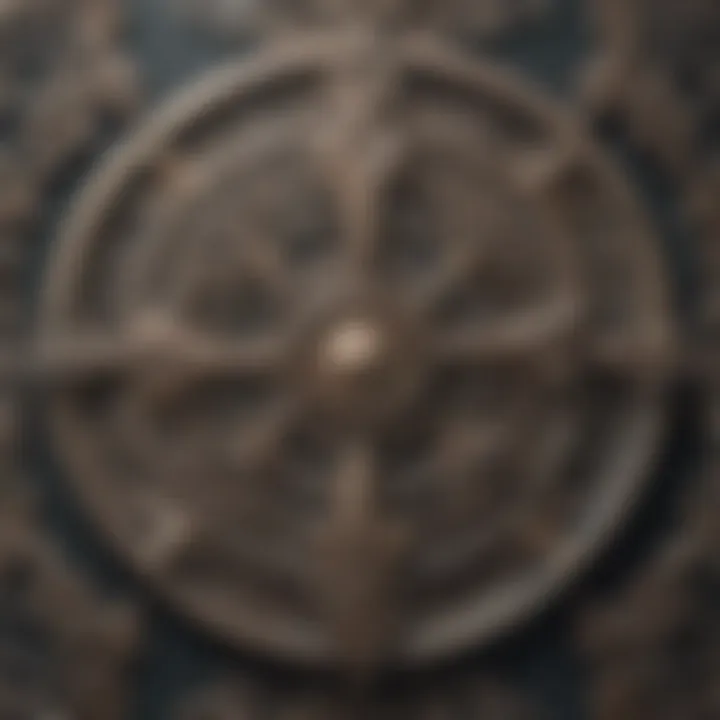
Files are the unsung heroes in the metalworking toolbox. They enable fine detailing, smoothing edges, and shaping the metal to perfection. When working with steel or brass, having a set of files with various shapes and gradations can enhance your outcomes significantly.
With the right file, one can transform a raw edge into a smooth complexion, ensuring that no faulty edges interfere with the beauty of your designs. Regular maintenance of files can tremendously maximize their efficiency.
Pliers
Pliers play a crucial role when it comes to gripping, bending, and manipulating metal during the process. Long-nosed pliers allow you to reach into tight spots and provide the necessary leverage for precision. Their grip helps secure metal pieces firmly, allowing you to work without the constant worry of slippage.
Their utility in managing dies and molds often goes overlooked, but each set contributes to creating accuracy. Plus, they help avoid excessive hand strain if you must twist or bend the metal.
Working with Dies and Molds
The importance of dies and molds cannot be understated in metal stamping. They stand as the blueprint for your design and contribute significantly to its outcome. Choosing the right dies can streamline the process, ensuring that you achieve consistency in your work.
Interestingly, using custom-made dies can drastically improve the overall quality of your product. However, understanding the compatibility of dies with the types of metal you choose is critical. This will help in avoiding mishaps during the stamping, thereby allowing you to focus on creativity rather than frustration.
Designing Your Stamp
Designing your own metal embossing stamp is a crucial step in the metalworking process. It serves as the foundation for everything that follows, enabling artisans to express their creativity while ensuring accuracy and clarity in the final product. When done right, a well-designed stamp can elevate a piece significantly, making it distinct and personal.
Before diving into the creation process, it's important to consider what the design will represent. This involves understanding both the aesthetic and functional aspects. The design should not only look appealing but also work effectively when stamped. Having a clear vision from the beginning can save time and materials down the line.
There are several elements to consider in designing your stamp:
- Purpose of the Stamp: Are you creating a stamp for personal use, for gifts, or for commercial products?
- Size and Shape: Will your design fit within a specific area? Consider, for example, that a small, intricate design may not show well on a large canvas, and vice versa.
- Text vs Images: Some designs may incorporate text, while others may be purely graphic. Think about the legibility of any text you include; certain fonts may not translate to metal well.
- Material Compatibility: The design may also need to factor in the type of metal you're working with, since different materials can bear impressions differently.
By addressing these considerations up front, one sets a solid groundwork for the actual construction of the stamp.
Creating Initial Sketches
Starting with initial sketches allows for an organic development of ideas. Grab some paper and a pencil, and start doodling. Donโt overthink it! Just let the creativity flow. If you have something clear in your mind, it can help focus your sketches.
When sketching, consider:
- Multiple Concepts: Draw several variations of your design. You never know what might resonate until you see it in front of you.
- Refining Your Ideas: After your initial sketches, select a few that catch your interest, and refine these further.
- Feedback: Share your sketches with trusted peers, friends, or fellow artists for feedback. Fresh eyes can provide insights you might have missed.
Transferring Designs to Metal
Once you have a finalized sketch, the next step is transferring your design to the metal. This transition can be quite delicate and requires attention.
Here is a general approach to transferring designs effectively:
- Trace the Design: Place your sketch underneath a thin sheet of metal. You may trace the design with a suitable etching tool or a light pencil to mark it on the metal surface.
- Use Carbon Transfer Paper: Place carbon transfer paper between your design and the metal. This way, pressing on the sketch will leave an imprint directly onto the metal.
- Direct Method for Intricate Designs: For more detailed work, consider using a laser engraver or CNC machine to ensure precision.
By carefully transferring your design, you set the stage for effective and successful embossing. Always remember that the more accurate the transfer, the cleaner the final emboss will be.
"Good design is all about making connections. The clearer and more intuitive those connections are, the better your product will resonate with its audience."
Designing with intention can set the stage for a quality metal embossing stamp that embodies your unique creativity.
The Embossing Process
The embossing process is the heartbeat of creating a metal embossing stamp. Itโs a finely-tuned operation that combines art, precision, and craftsmanship. For anyone eager to step into the world of metalworking, understanding this essential stage is key. Not only does it highlight the techniques involved, but it also illuminates the benefits that come with mastering each step.
Successful embossing requires meticulous preparation. A clean, well-finished metal surface is non-negotiable, as it directly influences the clarity and depth of the design. Additionally, having an organized workstation streamlines the process, enabling smooth transitions from task to task. Each element plays its part: the choice of technique, whether direct or heat stamping, impacts results differently. This knowledge can give you a competitive edge and elevate your creations.
Preparing the Metal Surface
Before you go hammering away, itโs vital to start with a metal surface thatโs as smooth as a babyโs bottom. Dirt, grime, or imperfections can ruin your design before you even get started. Gaining a good grip requires prepping your metal, which may involve several steps like cleaning, polishing, and ensuring the surface is as defect-free as can be.
Using sandpaper or a file could be your best mates here. They help refine the metal, making sure it's ready to accept the detailed impressions of your design. This attention to detail sets the tone, so do not rush through this phase. Remember, itโs about laying a solid foundation for the imprint.
Setting Up the Workstation
The workstation isnโt just a fancy term for your crafting table; itโs your command center. Organizing tools and materials is akin to setting the stage for a performance. When everything is within armโs reach, your focus remains on the creative process rather than chasing tools that seem to play hide and seek.
- Stable Surface: Make sure your table is steady to absorb the impact from hammers and tools.
- Lighting: Good lighting can make a world of difference. You donโt want to miss that tiny element in your design.
- Safety Gear: A pair of safety glasses and gloves make you look professional while keeping accidents at bay.
Embossing Techniques

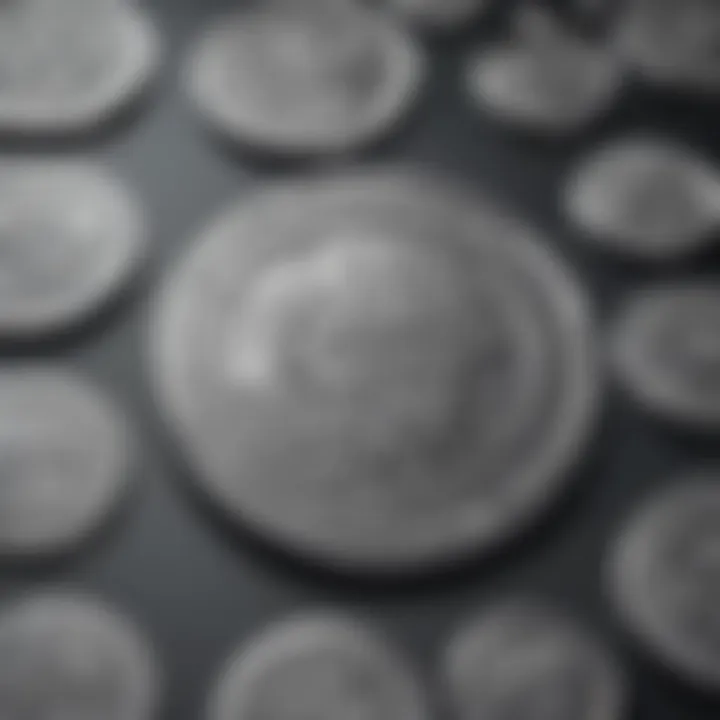
When it comes to the nitty-gritty of embossing, it helps to know the available techniques. They are the magic wand that transforms your ideas into tangible products. Two popular techniques stand out: direct stamping and heat stamping, both having distinct characteristics and advantages.
Direct Stamping
Direct stamping is all about that hands-on approach. It involves using a metal die that imprints your design directly onto the metal surface. One of the most appealing aspects of this method is its simplicity; you donโt need tons of equipment, just your stamp and a good hammer.
Key characteristic: One hit can deliver a clear, defined impression. The immediate feedback you get lets you see results as you go, which is why many artisans favor it. One of the unique features of direct stamping is the ability to work quickly on multiple pieces once you have your die prepared.
However, itโs not without its challenges. If not executed properly, you might end up with shallow or uneven impressions. Thus, practice and patience are vital. The learning curve might seem steep at first, but with time, you could develop dexterity that impresses even the most seasoned artisan.
Heat Stamping
Heat stamping, on the other hand, brings a whole new element to the table. As the name suggests, it involves heating the die to imprint the design into the metal. This method is especially useful for those intricate designs that require more detail and depth.
Key characteristic: The heat allows the metal to be more malleable, yielding cleaner impressions and finer details. It is perfect when you are working with thicker materials that might resist direct pressure.
A unique feature of this technique is that it opens doors to creativity; it allows for a broader range of design options. However, be cautious with the setup and ensure proper calibration of heat, as overheating could ruin the material. While heat stamping could be seen as a little bit more complex, it delivers impressive results worth the investment in time.
Finishing Touches
When it comes to crafting a metal embossing stamp, the finishing touches are not just the icing on the cake; they're what make the whole endeavor worthwhile. These final processes enhance both the aesthetic appeal and functional performance of your stamp. Neglecting these elements can lead to a lackluster result that neither you nor your clients would appreciate. Itโs in the finer details where quality truly shines through, ensuring longevity and satisfactory results in your projects.
Polishing Your Stamp
Polishing your stamp is akin to putting on the final coat of paint on a masterpiece. Itโs essential for ensuring your designs not only look professional but also feel smooth to the touch. Begin by selecting an appropriate polishing compound tailored to the type of metal you've used. For instance, if youโve chosen brass, consider using a metal polish specifically formulated for brass to prevent any potential discoloration.
- Start with a clean, dry cloth and apply a small amount of the chosen polish directly onto the stamp's surface.
- Use another cloth to gently buff the metal in circular motions. This technique not only brings out a brilliant shine but also evens out any minor imperfections that may have surfaced during the initial crafting process.
- Rinse away any residue with warm water and dry thoroughly.
This step is particularly important because a polished surface can significantly enhance the clarity of your stamped designs, making even the smallest details pop. Consider that a shiny finish works wonders when creating pieces intended as gifts or for commercial use. You want to avoid any unpleasant surprises during presentation, right?
Protecting the Stamp from Damage
Once the polishing work is done, itโs crucial to think about protecting your stamp. After all, the effort you put into crafting it shouldnโt go to waste due to careless handling or environmental wear. Here are a few strategies to keep your stamps in great shape:
- Store Properly: Always keep your stamps in a designated storage area, ideally in individual compartments to avoid scratching against one another.
- Use Oil: A light application of machine oil or mineral oil can provide a protective barrier against rust or tarnishing. A simple rub down with an oil-soaked cloth before and after each use can save you a lot of trouble down the line.
- Handle with Care: Whenever you use your stamp, ensure your hands are clean and dry. Grease from fingers can affect the stampโs finish, ultimately marring the beauty youโve worked so hard to achieve.
โAn ounce of prevention is worth a pound of cure.โ โ Benjamin Franklin
By incorporating these finishing touches, you guarantee that both your craftsmanship and your practices reflect the quality you aim for. Taking these extra steps may seem tedious and even unnecessary at times, but the results will speak volumes in both durability and appearance of your metal embossing stamp. For those passionate about design and metalworking, ensuring every element is polished and protected not only fulfills a professional standard but elevates your work to a whole new level.
Applications of Metal Embossing Stamps
Metal embossing stamps serve as more than mere tools; they are vessels of creativity and individuality. The applications of these stamps stretch far and wide, from the sentimental gestures in personalized gifts to the practical functions in various commercial fields. Understanding the importance of these applications can enhance both the artisan's craft and the consumer's experience, making the study of metal embossing stamps not only relevant but essential to modern design and craftsmanship.
Personalized Gifts and Items
Creating personalized gifts can take on many forms, but metal embossing adds a distinct touch that speaks volumes. Commonly, artisans leverage metal stamps to engrave names, dates, or messages onto keepsakes such as jewelry, keychains, or even serving utensils. Such personalization transforms ordinary items into cherished memories that can withstand the test of time.
For instance, imagine crafting a copper bracelet that bears the initials of a loved one. This not only showcases the artisan's skill but also creates a sentimental value the recipient will treasure.
When considering the process:
- Select the right metal: Copper and brass are popular choices due to their workability and aesthetic appeal.
- Choose a design: Whether itโs a name or a special symbol, find a motif that resonates.
- Emboss with care: A steady hand ensures the design comes out crisp and clear, making the gift even more special.
Every piece crafted holds a story unto itself, emphasizing the emotional connection formed through the art of metal embossing. This personal touch can be a game changer, elevating a simple gift to something of lasting significance.
Commercial Applications
On the commercial side, metal embossing stamps find a robust market presence. Many businesses utilize them for branding purposes, enabling them to stamp their logos on goods ranging from leather products to packaging materials. This not only enhances brand visibility but also adds a level of sophistication that is hard to replicate through standard printing methods.
Consider a boutique that offers high-end leather goods. By embossing their logo onto the items, they project an image of quality and attention to detail. The tactile experience of the embossed logo often draws customers inโquite literally, as it invites touch and engagement.
Moreover, the educational realm benefits as well. Schools and training centers encourage students in arts and crafts programs to explore metal stamping to cultivate fine motor skills and an eye for detail.
The benefits of commercial applications are manifold:
- Brand recognition: A well-placed stamp can make a significant impact on customer recall.
- Customer engagement: Touching an embossed item creates a connection that plain printing cannot.
- Innovative designs: Companies can experiment with various materials and textures to stand out in a crowded market.
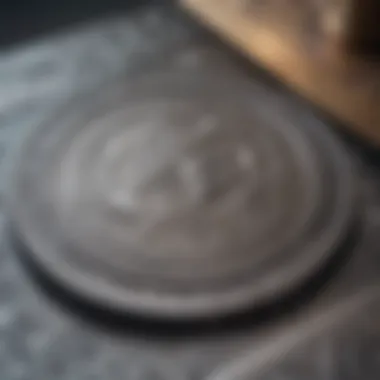
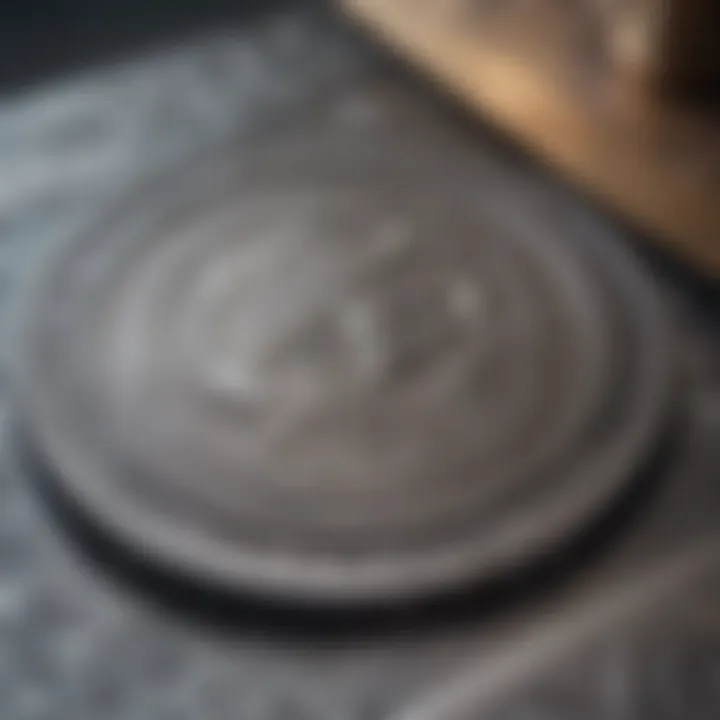
"In a world where branding matters, metal embossing adds a touch that can set you apart."
Businesses of all shapes and sizes have begun to realize the value of embossing as part of their marketing arsenal. Whether crafting unique promotional items or simply enhancing product aesthetics, the art of metal embossing can dramatically improve commercial success.
In summary, both personalized gifts and commercial applications underscore the versatility and significance of metal embossing stamps. The key lies in understanding how these tools can enhance creativity, allow for personal expression, and foster brand identity in today's competitive landscape.
Troubleshooting Common Issues
In any craft, especially one as meticulous as metal embossing, encountering problems is part and parcel of the process. Understanding how to troubleshoot common issues can save artisans significant time and frustration. This section not only highlights the key quality problems that may arise during the use of metal embossing stamps but also provides solutions to rectify these defects. Knowing how to identify and resolve issues enhances the overall quality of your work and ensures that your designs achieve the desired aesthetic.
Identifying Stamp Quality Problems
Spotting defects in your metal embossing stamp is crucial. A simple issue can lead to dissatisfaction in the final product. Here are some key problems to look out for:
- Inconsistent Depth of Imprint: If you notice that certain parts of the impression are shallower than others, the die might not be evenly shaped or is being applied with inconsistent pressure.
- Faded or Blurry Images: This often indicates that either the stamp is dirty or the design was not adequately transferred to the metal. If your stamp doesnโt maintain a crisp outline, it could be time for a clean-up or a redesign.
- Damaged Edges: If you see chipping or rough edges on your stamps, this might be a sign of the tool being used inappropriately or unsuitable material.
- Misalignment: When impressions are not in the correct position, the setup on your workstation may need adjustment. Misalignment can be due to negligence during the setup process.
An attentive eye can often catch these discrepancies early, enabling you to address problems before they spiral into bigger issues.
Solutions for Common Defects
Now that you've identified the problems, here are some practical ways to address them:
- Adjusting Pressure: When creating an imprint, make sure to apply a steady and even pressure distribution. Consider using a hammer with a cushioned face to help with consistent strikes.
- Cleaning Your Stamp: Regular maintenance is key. Use a soft brush or cloth to remove debris, and inspect the stamp frequently to prevent dirt from affecting your designs.
- Refining the Design: If imprints appear faded or blurry, it might be wise to reassess the design's complexity. Simpler designs often translate better into metal work.
- Re-aligning the Workstation: Before starting, ensure that all your equipment is on a level surface. Also, double-check that the metal piece is positioned correctly under the stamp. A misaligned setup can compromise your entire project.
"Quality in craftsmanship comes from attention to details. Address the small issues before they become larger problems."
By addressing issues promptly, you can not just salvage a project but also enhance your skills as a metalworker. Recognition of problems and having a set of solutions at hand allows for a smoother and ultimately more gratifying crafting experience.
Sustainability in Metalworking
As the world becomes more conscious of environmental concerns, the concept of sustainability in metalworking is gaining traction across industries. In the realm of crafting metal embossing stamps, adopting sustainable practices isn't just a trend; it's a responsibility that can lead to tangible benefits. By prioritizing sustainability, artisans not only contribute to the well-being of the planet but also embrace innovative approaches that can enhance their craft and reputation.
Choosing Sustainable Materials
When selecting materials for metal embossing, opting for sustainable choices is vital. Explore recycled metals, which have a significantly lower environmental impact compared to virgin materials. For instance, using recycled aluminum not only reduces energy consumption during production but also minimizes waste. Here are some sustainable options to consider:
- Recycled metal sources: Many suppliers offer metals that are made from recycled content, such as aluminum or copper, which conserves resources.
- Local sourcing: Whenever possible, obtain materials from local suppliers. This reduces transportation emissions and supports local economies.
- Eco-friendly coatings: If finishes are needed, consider using coatings that are non-toxic and biodegradable, which reduces harmful chemical exposure.
Emphasizing sustainable materials in crafting not only showcases responsibility but can also appeal to a growing consumer base interested in eco-friendly products.
Waste Management Practices
Proper waste management is another cornerstone of sustainability in metalworking. The embossing process can generate various by-products, and how these are handled is crucial. Implementing effective waste management practices can help mitigate the negative aspects of metalworking. Here are some strategies:
- Recycling scrap metal: Regularly collect any offcuts or defective pieces. Recycle these materials to ensure they don't end up in landfills.
- Responsible disposal: For any non-recyclable waste, partner with certified disposal services that adhere to environmental standards.
- Inventory control: Keep track of materials and usage to minimize over-purchasing and waste generation.
Implementing these waste management tactics not only enhances efficiency but also reflects a commitment to sustainability that can resonate with consumers and clients alike.
"A green approach not only protects the environment but can also revitalize your craft and inspire innovative thinking."
By integrating sustainability into the metal embossing stamp production process, artists can carve out a niche that respects both the earth and their craft, appealing to environmentally aware consumers and fostering a sense of community responsibility.
End
The conclusion serves as a capping stone, neatly tying together the intricate threads of knowledge woven throughout this article on metal embossing stamps. The importance of this section lies in its ability to encapsulate the multitude of facets discussed and provide a clear path for moving forward.
Understanding how to create a metal embossing stamp isn't simply a craft; it's a gateway into a world where design meets functionality. From selecting the right tools and materials to troubleshooting issues, every step in the process contributes to the final product's quality and usability. This reinforces the viability of metal embossing as a means of expression, allowing individuals to create personalized items or commercial products tailored to specific tastes and needs.
Key benefits include not only the enhancement of craftsmanship but also the potential for creativity in various professional fields such as fashion design, styling, and retail. Embracing this skill, therefore, opens a treasure chest of possibilities. Additionally, being mindful of sustainability in metalworking has implications that extend beyond personal artistry. Adopting eco-friendly practices reaffirms the commitment toward a more responsible form of craftsmanship.
The essential elements covered in this guide also highlight the methodological approach required in metal embossing. The combination of technique and tool mastery ultimately defines the quality of oneโs output, contextually situating metalworking within broader artistic trends today.
"Craftsmanship lies in the details; metal embossing is no exception to this rule."
Recap of Key Points
- Essential Tools: Understanding the tools necessary for metal embossing is foundational.
- Design Process: Developing a strong design is crucial for a successful embossing stamp.
- Embossing Techniques: Familiarity with various embossing methods aids in achieving desired results.
- Troubleshooting: Identifying and resolving common issues can save time and resources.
- Sustainability: Incorporating eco-friendly practices enhances not just the craft but also personal ethics in creativity.
Encouragement for Further Exploration
Those who find enjoyment in the art of metal embossing should not hesitate to explore deeper avenues within this creative endeavor. Attend workshops, join online forums like those on Reddit, or participate in local craft fairs to engage with others who share the same passion. This is essential not just for skill enhancement but also for networking opportunities that can lead to collaborations.
Consider branching out beyond stamps to other metalworking projects. As confidence builds, challenge yourself with more complex designs or materials, allowing your artistic expression to evolve. Stay informed about new trends in the craft and embrace innovative techniques that may come along the way.
In the vast universe of fashion and design, keep nurturing that creative spark. Thereโs always something new to learn, and every bit of knowledge amassed contributes to becoming a well-rounded artisan. With each embossed piece, you're not just creating; you're narrating stories through metal, adding your unique voice to the rich tapestry of craftsmanship.